According to Gartner, smart factories are one of the top 10 strategic technology trends for the manufacturing industry. To fully embrace this trend, manufacturing leaders must consider their connectivity infrastructure. Connectivity is the backbone of smart factories, as it allows facilities to integrate sensors and robotics to automate operations.
Private 5G networks provide reliable, high-capacity connectivity infrastructure to support new technologies and create a more streamlined and automated manufacturing ecosystem for smart factories. This level of enhanced connectivity results in increased line efficiency, higher-quality products, and greater customer value.
Current infrastructure limits technological advancement
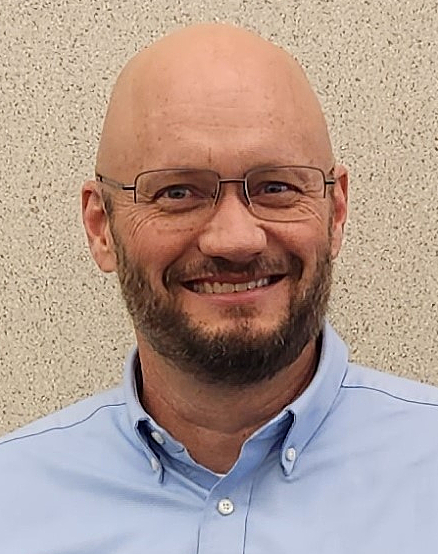
Manufacturing facilities using complex legacy systems and stationary connectivity equipment limit where machinery can be laid out throughout the factory. For example, it’s time-consuming and costly for a facility with miles of embedded Ethernet cables and Wi-Fi drop points to relocate connected machines and equipment since connectivity correlates to specific points on the factory floor.
Fixed connectivity also makes it more challenging to adopt smart factory solutions such as autonomous robots, as Ethernet and Wi-Fi don’t provide consistent connections throughout large factories. If an autonomous robot is tasked with moving items around a factory and hits a connectivity “dead zone,” it may stop, holding up the manufacturing process until someone moves the robot back into a connected area.
An additional concern is that if a factory experiences an outage, the entire system could shut down. It is difficult to run diagnostics on Ethernet, Wi-Fi, and limited cellular without a skilled worker physically connecting to a server. The manual process required to troubleshoot and reconnect the network increases downtime and reduces the effectiveness of automated and autonomous solutions.
Considerations for deploying private 5G networks
Alternatively, private 5G networks offer a consistent, reliable, and flexible infrastructure that can handle the data-intensive applications and technologies that make up smart factories. Since it uses a dedicated bandwidth, it can connect multiple devices and provide real-time data collection, analysis, and application. Private 5G networks can also be customized to meet specific organizational needs, which allows for greater control, adaptability, and security.
Most importantly, these networks can scale as operations grow or technologies change, future-proofing facilities for long-term success.
When exploring how to upgrade connectivity infrastructure to transform a facility into a smart factory, manufacturing leaders should consider:
– The best mix of connectivity infrastructure: Every factory will need a different combination of connectivity options based on budget and existing technology. For example, an 80% private 5G wireless, 10% hardware, and 10% Wi-Fi mix could meet the needs of a changing manufacturing floor, with private 5G expanding the opportunity to integrate with new devices and machines. Other facilities may need more hardware or more Wi-Fi to accommodate budget constraints or to work with legacy technologies they depend on for existing operations.
– Speed and latency requirements: With their faster speeds and lower latency, private 5G networks support the real-time data processing needed for autonomous robots and connected tools. For example, manufacturers can attach sensors to welding equipment to capture data to train an algorithm for the best weld and use sensors to analyze machine vibration and sound data to detect issues before they cause downtime.
– Current needs and future integrations: Private 5G networks allow manufacturers to more easily move connected devices and machines throughout the factory floor for optimal line layouts. This adaptability is more cost-effective, especially compared to Ethernet, which requires complete rewiring with each new configuration.
Benefits beyond the factory floor
Private 5G networks are essential to transforming today’s manufacturing facilities into smart factories by accelerating and supporting edge computing, real-time location systems, advanced inventory management solutions, line automation, and autonomous machines. These next-gen technologies help manufacturers adapt to changing market and labor conditions, streamline workflows, and improve cost efficiencies.
This ensures that customers get the best possible product when they need it, and it gives manufacturers a long-term competitive edge.
Jason Wallin is the Principal Architect for John Deere within the Global Information Technology group. He is focused on establishing the organization’s intelligent edge vision to enable the factory of the future and developing the strategy to deliver this vision. Wallin has held numerous roles within John Deere, the Department of Defense, and the larger IT industry. He is focused on advanced industrial networking technologies, communications security, tech-stack development, radio frequency engineering, cloud native computing, engineering leadership, and operational technology leadership.