This article is taken from a new editorial report on the state of IoT in the supply chain sector, released this month (January 2023). The report discusses the potential Industry 4.0 upside for the supply chain sector in all its disjointed promise, with some history and context, and a long discussion about the new maturity of the IoT market – and its need to accept its role as a useful addition to Industry 4.0, and not the story by itself.
It includes a number of interviews and case studies besides, plus forecasts and figures about tech takeup in the supply chain market. The report – called, IoT tracking in the supply chain and logistics industry – how IoT grew up and got real, in the hardest industry of them all – is available to download here (or by clicking on the image below). An introduction section has already been posted online, here; further articles from the report may also appear online.
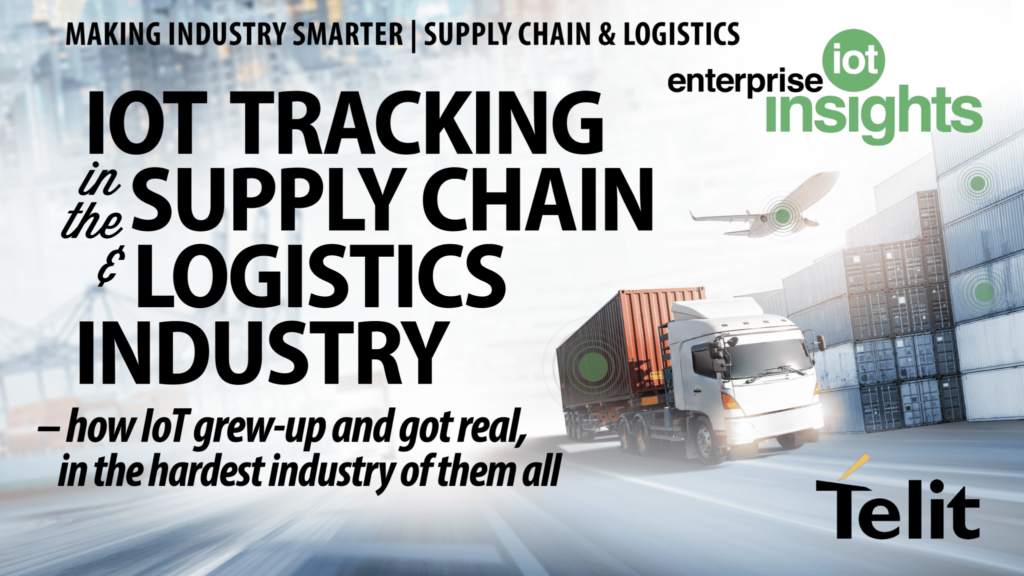
The supply chain is tough, and getting tougher. As a first port of call, right out of the gate, we should meet Erich Hugo from US-based DeltaTrak; his firm has been in the tracking game for three decades already, originally supplying manual data loggers to logistics firms for post-analysis of goods in transit – the same ‘things’ now being connected by any number of IoT technologies, by any number of IoT firms, to get real-time readouts on their position and condition.
Hugo wants us to take a step back, momentarily. “Logistics contributes about a third of the world’s GDP,” he says. “It is also one of the oldest industries in the world. I mean, it started 4,000 years BC; we talk about travellers on the Silk Road between Asia and Europe, and so on. It is not something that just suddenly became relevant in the 20th century, since it was discovered by technology. There is no other industry with the same rules and regulations.”
We should interrupt, briefly, and check those numbers. The size of the global logistics industry ranges from $8 trillion to $12 trillion, annually; global gross domestic product (GDP) was $96 trillion in 2021, according to the World Bank – which puts the contribution from logistics at between 8.3 percent and 12.5 percent. German market data company Statista (left) calculates the industry was worth $8.4 trillion in 2021/22, equivalent to 10.7 percent of global GDP.
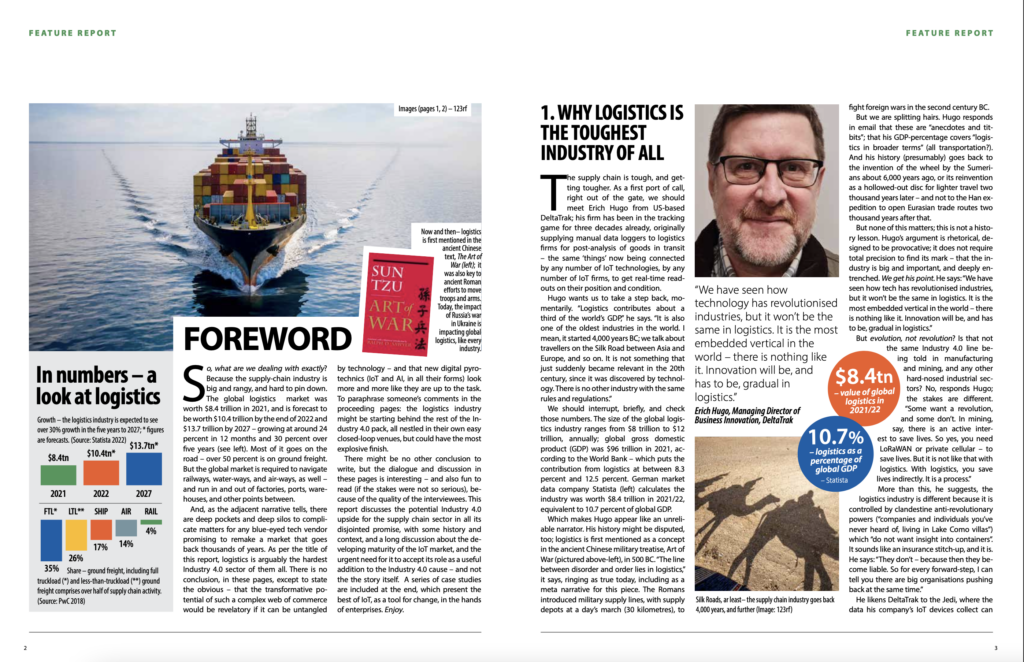
Which makes Hugo appear like an unreliable narrator. His history might be disputed, too; logistics is first mentioned as a concept in the ancient Chinese military treatise, Art of War, in 500 BC. “The line between disorder and order lies in logistics,” it says, ringing as true today, including as a meta narrative for this piece. The Romans introduced military supply lines, with supply depots at a day’s march (30 kilometres), to fight foreign wars in the second century BC.
But we are splitting hairs. Hugo responds in email that these are “anecdotes and titbits”; that his GDP-percentage covers “logistics in broader terms” (all transportation?). And his history (presumably) goes back to the invention of the wheel by the Sumerians about 6,000 years ago, or its reinvention as a hollowed-out disc for lighter travel two thousand years later – and not to the Han expedition to open Eurasian trade routes two thousand years after that.
But none of this matters; this is not a history lesson. Hugo’s argument is rhetorical, designed to be provocative; it does not require total precision to find its mark – that the industry is big and important, and deeply entrenched. We get his point. He says: “We have seen how tech has revolutionised industries, but it won’t be the same in logistics. It is the most embedded vertical in the world – there is nothing like it. Innovation will be, and has to be, gradual in logistics.”
But evolution, not revolution? Is that not the same Industry 4.0 line being told in manufacturing and mining, and any other hard-nosed industrial sectors? No, responds Hugo; the stakes are different. “Some want a revolution, and some don’t. In mining, say, there is an active interest to save lives. So yes, you need LoRaWAN or private cellular – to save lives. But it is not like that with logistics. With logistics, you save lives indirectly. It is a process.”
More than this, he suggests, the logistics industry is different because it is controlled by clandestine anti-revolutionary powers (“companies and individuals you’ve never heard of, living in Lake Como villas”) which “do not want insight into containers”. It sounds like an insurance stitch-up, and it is. He says: “They don’t – because then they become liable. So for every forward-step, I can tell you there are big organisations pushing back at the same time.”
He likens DeltaTrak to the Jedi, where the data his company’s IoT devices collect can be used, in extreme cases, as expert witness in insurance disputes about damaged or delayed freight, but where the prospect of higher insurance premiums for goods producers and logistics providers means this lightsaber insight is only utilised tactically as a rebellious force, kept instead for skirmishes in the outer rim. “We can protect people, but we can’t fight their war,” says Hugo.
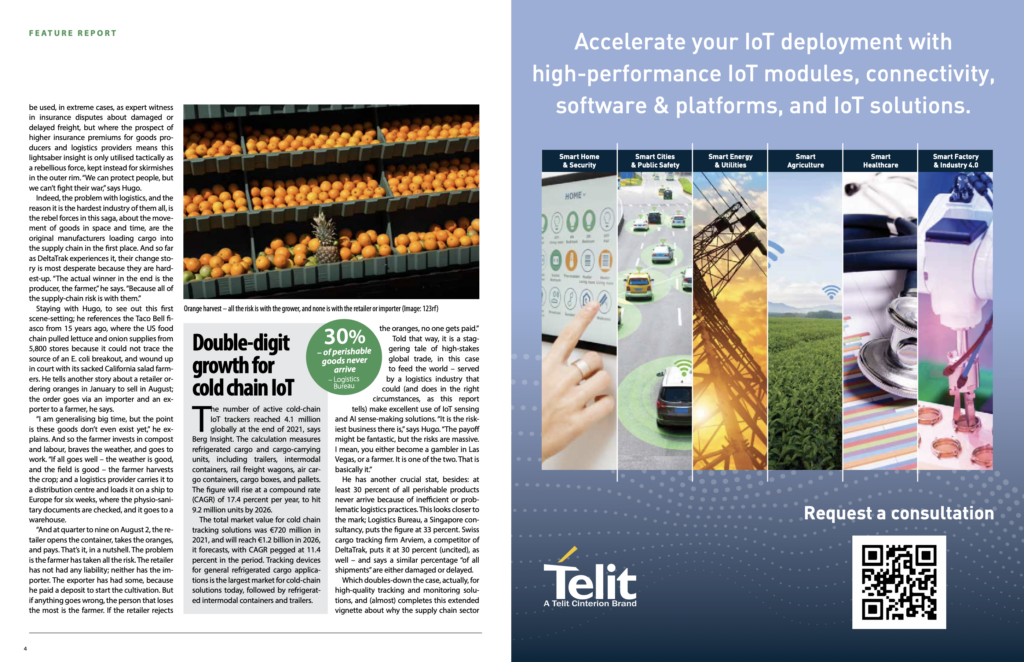
Indeed, the problem with logistics, and the reason it is the hardest industry of them all, is the rebel forces in this saga, about the movement of goods in space and time, are the original manufacturers loading cargo into the supply chain in the first place. And so far as DeltaTrak experiences it, their change story is most desperate because they are hardest-up. “The actual winner in the end is the producer, the farmer,” he says. “Because all of the supply-chain risk is with them.”
Staying with Hugo, to see out this first scene-setting; he references the Taco Bell fiasco from 15 years ago, where the US food chain pulled lettuce and onion supplies from 5,800 stores because it could not trace the source of an E. coli breakout, and wound up in court with its sacked California salad farmers. He tells another story about a retailer ordering oranges in January to sell in August; the order goes via an importer and an exporter to a farmer, he says.
“I am generalising big time, but the point is these goods don’t even exist yet,” he explains. And so the farmer invests in compost and labour, braves the weather, and goes to work. “If all goes well – the weather is good, and the field is good – the farmer harvests the crop; and a logistics provider carries it to a distribution centre and loads it on a ship to Europe for six weeks, where the physio-sanitary documents are checked, and it goes to a warehouse.
“And at quarter to nine on August 2, the retailer opens the container, takes the oranges, and pays. That’s it, in a nutshell. The problem is the farmer has taken all the risk. The retailer has not had any liability; neither has the importer. The exporter has had some, because he paid a deposit to start the cultivation. But if anything goes wrong, the person that loses the most is the farmer. If the retailer rejects the oranges, no one gets paid.”
Told that way, it is a staggering tale of high-stakes global trade, in this case to feed the world – served by a logistics industry that could (and does in the right circumstances, as this report tells) make excellent use of IoT sensing and AI sense-making solutions. “It is the riskiest business there is,” says Hugo. “The payoff might be fantastic, but the risks are massive. I mean, you either become a gambler in Las Vegas, or a farmer. It is one of the two. That is basically it.”
He has another crucial stat, besides: at least 30 percent of all perishable products never arrive because of inefficient or problematic logistics practices. This looks closer to the mark; Logistics Bureau, a Singapore consultancy, puts the figure at 33 percent. Swiss cargo tracking firm Arviem, a competitor of DeltaTrak, puts it at 30 percent (uncited), as well – and says a similar percentage “of all shipments” are either damaged or delayed.
Which doubles-down the case, actually, for high-quality tracking and monitoring solutions, and (almost) completes this extended vignette about why the supply chain sector – also linking neater standalone change-projects in factories and warehouses, in between – is so hard. But before we get to the gospel chorus, to bring light to these supply-chain blues, there is a further verse about how logistics is getting harder, as well.
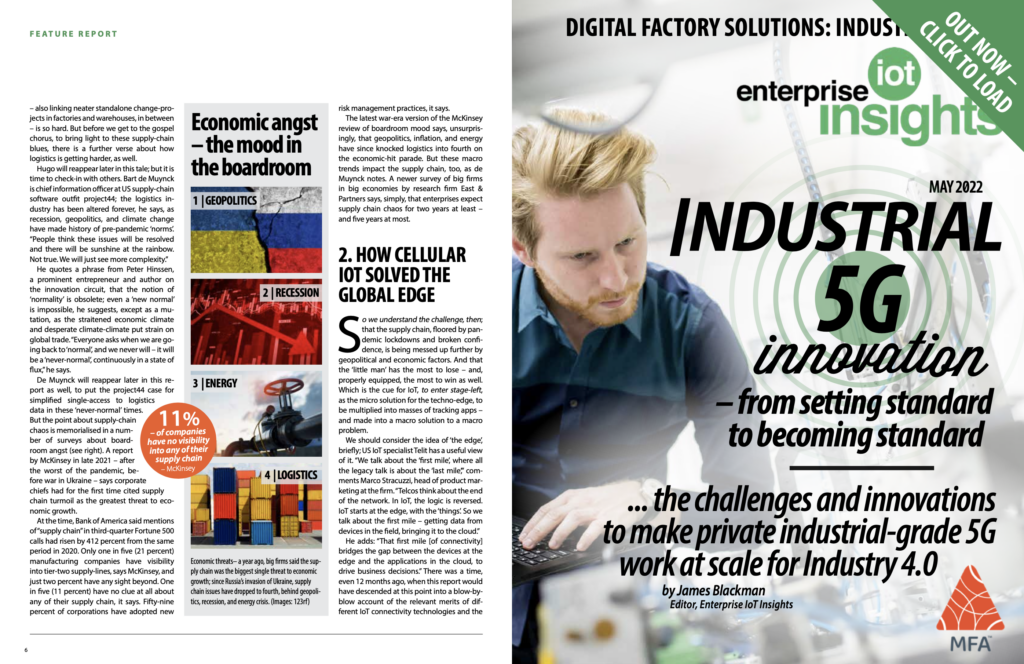
Hugo will reappear later in this tale; but it is time to check-in with others. Bart de Muynck is chief information officer at US supply-chain software outfit project44; the logistics industry has been altered forever, he says, as recession, geopolitics, and climate change have made history of pre-pandemic ‘norms’. “People think these issues will be resolved and there will be sunshine at the rainbow. Not true. We will just see more complexity.”
He quotes a phrase from Peter Hinssen, a prominent entrepreneur and author on the innovation circuit, that the notion of ‘normality’ is obsolete; even a ‘new normal’ is impossible, he suggests, except as a mutation, as the straitened economic climate and desperate climate-climate put strain on global trade. “Everyone asks when we are going back to ‘normal’, and we never will – it will be a ‘never-normal’, continuously in a state of flux,” he says.
De Muynck will reappear later in this report as well, to put the project44 case for simplified single-access to logistics data in these ‘never-normal’ times. But the point about supply-chain chaos is memorialised in a number of surveys about boardroom angst (see report). A report by McKinsey in late 2021 – after the worst of the pandemic, before war in Ukraine – says corporate chiefs had for the first time cited supply chain turmoil as the greatest threat to economic growth.
At the time, Bank of America said mentions of “supply chain” in third-quarter Fortune 500 calls had risen by 412 percent from the same period in 2020. Only one in five (21 percent) manufacturing companies have visibility into tier-two supply-lines, says McKinsey, and just two percent have any sight beyond. One in five (11 percent) have no clue at all about any of their supply chain, it says. Fifty-nine percent of corporations have adopted new risk management practices, it says.
The latest war-era version of the McKinsey review of boardroom mood says, unsurprisingly, that geopolitics, inflation, and energy have since knocked logistics into fourth on the economic-hit parade. But these macro trends impact the supply chain, too, as de Muynck notes. A newer survey of big firms in big economies by research firm East & Partners says, simply, that enterprises expect supply chain chaos for two years at least – and five years at most.
The rest of this article appears in a new editorial report, available to download for free here.